Manufacturing jobs come in all shapes and sizes. From machine operators to quality control specialists, maintenance technicians to production managers, each crucial role requires specific skills and knowledge.
Despite this diversity, they all have one thing in common: well-trained workers produce better products. Training in manufacturing is crucial for ensuring high manufacturing quality and operational success.
But it’s not only manufacturing quality that benefits from training. What else, you ask?
In this article, we’ll highlight the five main reasons why training is important for manufacturing. From safety and operational efficiency to quality and compliance issues, employee training is an essential part of modern manufacturing.
Table of Contents
- Communication in manufacturing
- Top 5 reasons why is training important
- How to decrease cost in manufacturing
- FAQ
Communication in manufacturing
It can be difficult for manufacturers to communicate with operators directly. Frontline employees on the shop floor often don’t have corporate phones, computers, and company emails. Shift and production line crews may only be reached with lunch room notice boards and information that is passed through daily shift meetings.
To be successful, operators need to be connected with the latest performance data. They need safety and operations updates. They also need to have easy access to documentation to maintain high quality and meet compliance requirements.
With a digital workplace solution built for the manufacturing sector, leaders can ensure operators have standard operating procedures (SOPs), machine schematics, checklists, and company updates at their fingertips. Making communication more streamlined across the shop floor will optimize health and safety processes as well as compliance tracking.
Streamlining communication in this way not only keeps employees informed but also enhances the impact of training initiatives. When workers receive consistent and relevant information, training becomes more effective, leading to improved safety and compliance.
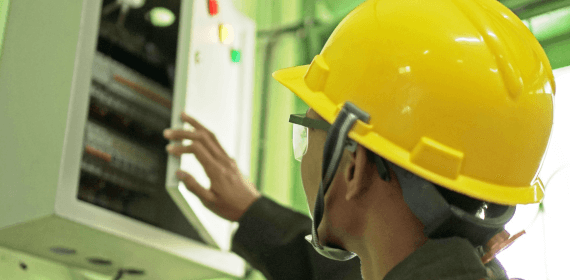
Why is training important for manufacturing? Top 5 reasons.
Continuous improvement
Who knows the manufacturing line better than its operators? Small, incremental changes increase efficiency and keep lines running smoothly. Many operators have the inherent drive to make small changes or offer suggestions to line managers for improvement.
Training operators to have a continuous improvement mindset makes sure that all workers understand their role in process optimization. They’ll all be aware that they can have the freedom and support to suggest changes and contribute to the enhancement of processes.
Seeing their ideas implemented boosts morale, motivation, and employee engagement, making staff members feel valued and invested in their work. This sense of ownership contributes to higher job satisfaction and productivity, ultimately leading to better manufacturing quality.
Updates to processes, SOPs, and new machines
When processes are updated or new machines are installed, training is required to get all staff up to speed. It isn’t enough to simply send an email or post an update on the bulletin board.
To make sure all staff understand the requirements of the change and how it affects their work is critical. Training methods should match the complexity of the change. For minor updates, self-paced online courses might be effective. For significant changes or new machinery, hands-on training provides practical experience.
Effective training makes sure that employees are capable of using new processes and machines efficiently, reducing the risk of operational downtime and errors.
Changes to regulations and compliance
Industries across the manufacturing landscape are seeing a rising need for regulations and compliance. Meeting these changing requirements is costly: from updates to documentation, processes, and equipment, to training staff on staying compliant.
Having a robust training strategy that can quickly adapt to changing regulations will ensure that all staff receive regulatory and compliance-related training quickly and effectively. The most streamlined way to disseminate training is through a digital training platform, where staff can access new courses when and where they want.
This helps in maintaining high standards of quality and compliance while avoiding penalties associated with non-compliance.
Safety reminders, updates, and re-training
Across all companies in manufacturing, regular safety training is vital for maintaining a safe work environment and preventing accidents. This includes periodic refresher courses and updates on new safety protocols.
For compliance-heavy industries, ensuring that all staff are up-to-date with the latest safety procedures has real implications for worker well-being and regulatory adherence. Continuous safety training also helps in identifying potential hazards early and mitigating risks before they lead to incidents.
This contributes to enhanced safety and efficiency on the factory floor, reducing the likelihood of costly accidents and improving overall productivity.
Skill development for the future of work
New technologies and automation are evolving faster than ever. As industrial robotics and automation become increasingly prevalent, training must focus on equipping employees to work effectively with these advanced systems.
Job training programs should include education on the latest automation processes and AI-driven tools. This includes learning about the functions of advanced manufacturing robots or AI-powered systems that offer enhanced flexibility and precision.
This rise in automation brings about new job roles and skill requirements. Training should address these changes by providing employees with future-proof skills such as robot programming, maintenance, data analysis, and process optimization, preparing them for the evolving job landscape.
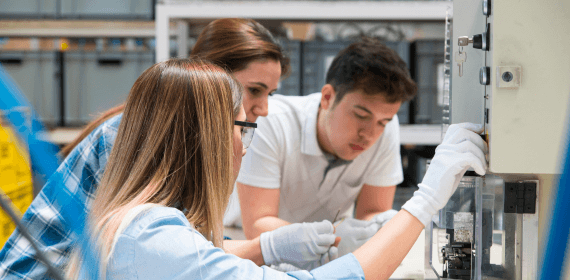
This is how training can decrease cost in manufacturing
Higher quality, less variation
Well-trained employees are more skilled at following SOPs and using machinery correctly, which minimizes production errors and defects. Training ensures that all workers have the same knowledge and skills, leading to uniform quality standards and fewer variations in the final product. This reduces the need for rework and enhances overall manufacturing quality.
Better efficiency and optimized processes
Training helps manufacturing team members understand and execute processes more efficiently, leading to less downtime and increased throughput. This means faster production cycles and better use of resources.
Proper training on machinery operation maximizes equipment performance and reduces maintenance costs. With soaring energy prices, every bit of efficiency earned is crucial. Investing in training will lead to more efficient, optimized production processes.
Fewer mistakes
With comprehensive training, both new employees and veterans are better equipped to handle unexpected issues or troubleshoot problems effectively, reducing the likelihood of costly mistakes.
A trained shop-floor is better at following procedures and using equipment correctly, which minimizes errors that can lead to decreased efficiency. Additionally, employees who make fewer mistakes experience less stress and are more motivated to work and take responsibility.
Increased safety and accident prevention
Regular safety training and updates help prevent accidents and injuries by ensuring employees are aware of and follow the latest safety protocols.
Maintaining high safety standards also helps manufacturing companies avoid costly fines and legal issues associated with non-compliance with safety regulations and documentation, contributing to overall cost savings.
Training for the future of the manufacturing industry
Looking towards the future, the potential for manufacturing jobs seems promising. As long as manufacturing organizations put workforce education first to identify skill gaps and training needs.
As automation handles more repetitive and hazardous tasks, workers in manufacturing are freed to focus on problem solving, critical thinking, and creative tasks.
Training must support this transition by developing skills in problem-solving, innovation, and process improvement, aligning with the evolving nature of manufacturing work.
With automation reshaping job roles, it’s crucial to prepare employees for new types of work. This includes upskilling for roles in automation and AI management and adapting to the changes in job functions brought about by technological advancements.
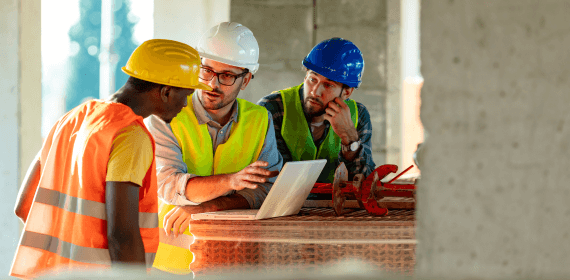
Want to learn more?
Getting your manufacturing plant prepared for the jobs of tomorrow needs a training strategy built for the future. Reach out to one of our experts to learn more about how iTacit can reshape your shop-floor training landscape with manufacturing LMS.
Frequently Asked Questions
How do I choose the right manufacturing training program for my shop-floor staff?
To choose the most effective training program, first identify what skills your staff need (e.g., technical skills, soft skills, safety, communication, etc.) and set clear training goals. Use digital tools like a digital employee platform to make training flexible and accessible.
Make sure the training materials are up-to-date and relevant to your operations, and include options for continuous learning with regular updates.
Lastly, ensure the training integrates well with your current systems and gather feedback from employees to improve the training through surveys and regular assessments.
What methods are most effective for delivering training in manufacturing?
Effective training methods include using digital tools such as employee apps on mobile devices and learning management systems (LMS) for easy, flexible learning. Virtual reality (VR) and augmented reality (AR) can provide hands-on practice with equipment and manufacturing processes.
Blended learning, which combines online and in-person training, is also powerful for knowledge retention. And, of course, continuous learning through regular updates and refresher courses helps keep skills fresh and relevant.
These best practices make sure that job training opportunities are engaging and meet the needs of your manufacturing staff.
How do I help new hires follow training processes in my manufacturing facility?
To help new hires follow the right training process, provide them with a structured onboarding program with clear steps and objectives to develop necessary skills.
Use digital tools for easy access to training materials, and pair new hires with experienced skilled workers for hands-on learning. Regular check-ins and feedback sessions will address any issues and ensure that training is effective and up-to-date.